Inventory management can be especially tricky for companies that need to keep track of spare parts. Whether an auto body shop, a construction company, or a manufacturer, certain businesses can’t complete their work unless they have the right spare parts on hand.
An optimized spare parts inventory management system is essential for companies that stock high volumes of parts inventory. This article will reveal six parts inventory management best practices your company can implement today.
1. Organize and tag every spare part
Managing spare parts inventory starts with physically organizing your parts. When organizing parts, it’s important to consider what parts can be grouped together for maximum convenience and ease of use. This will look different for every business.
Begin by physically tidying every inch of your storage space. Organize shelves, label bins, and rethink where you’re storing certain items. Essentially, you’ll want to review your inventory storage strategy top to bottom, ensuring that you’re making your warehouses, shelves, stockrooms, and storage units are arranged as logically as possible.
Once your storage space is sufficiently streamlined, it’s time to physically label your inventory. Inventory management software can automate that process, saving you tons of time, money, and stress. If you use the Sortly inventory app, you can generate barcode and QR code labels for your inventory and link them to corresponding inventory details.
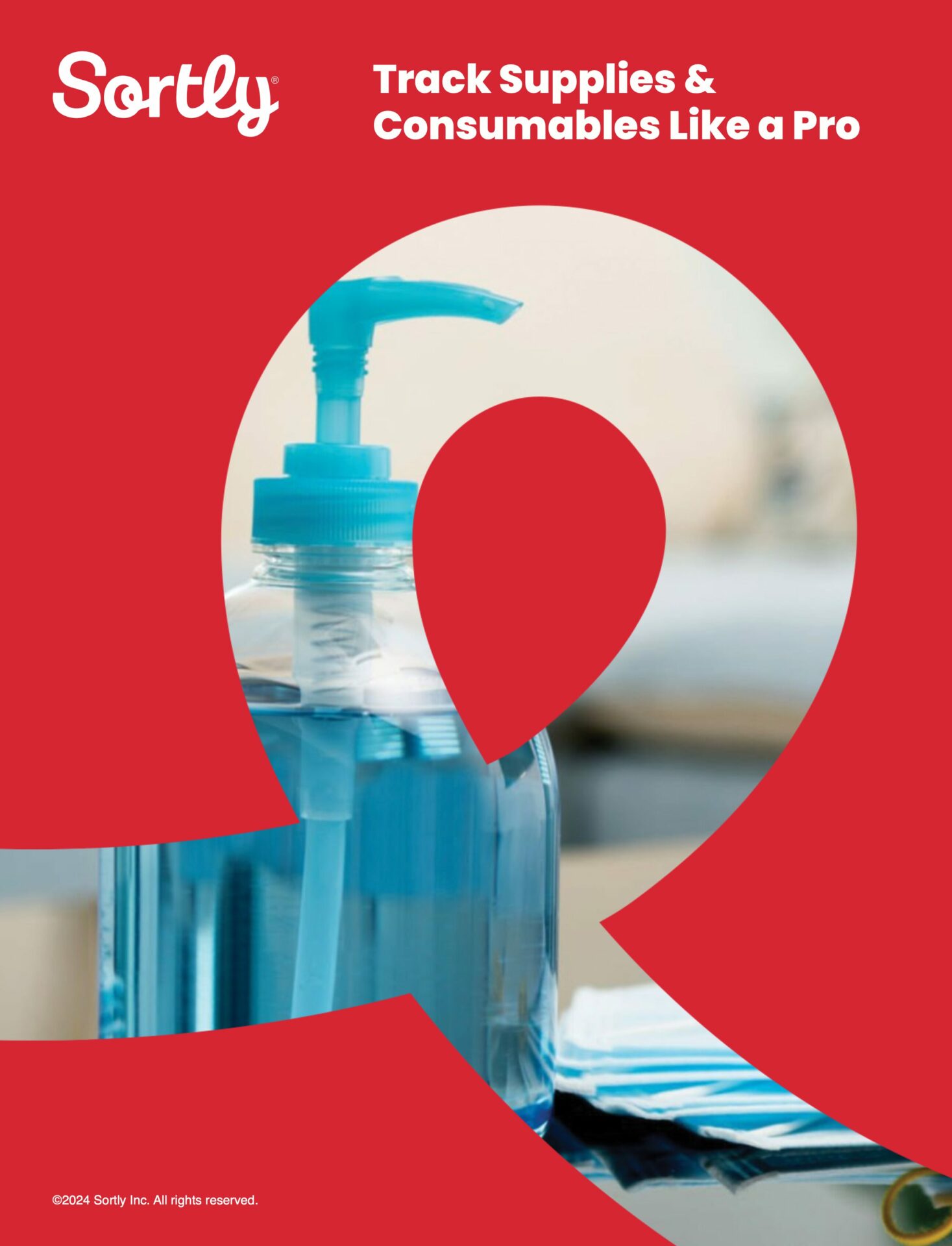
Free Ebook: Track Supplies & Consumables Like a Pro
This easy, comprehensive guide can help you:
- Create an inventory list for supplies and consumables
- Automate reordering with alerts and expiration reminders
- Perform inventory audits for consumable inventory
2. Create a parts inventory list
Whether you barcode or QR code your inventory, you should absolutely create a complete inventory list that details every single thing your business has on hand. If you stock lots of spare parts, you may also want to include parts you only buy when necessary. That way, it’ll be easy for your team to search for these items and confirm if you have any leftovers from a special project.
If you’re using inventory management software, you can create your inventory list as you sync existing or generate new barcodes and QR codes. For example, with an app like Sortly, you can easily create custom fields to track details that matter to you, along with all the usual categories, including item name, serial number, SKU, color, location, value, and price.
What’s more, the best inventory management software makes it easy to track spare parts across multiple locations, like company cars, storage closets, or offsite warehouses.
Even if you aren’t adopting a barcode inventory system to manage your spare parts, you still need to maintain an updated inventory list. Of course, you can always do this manually or using an inventory spreadsheet.
No matter how you maintain your inventory list, this report can help you conduct inventory audits and end-of-year inventory counts.
Related: How do you keep track of inventory in Excel?
3. Establish a clear parts reordering process
Now that your inventory is organized, barcoded, and itemized on an inventory list, it’s time to turn your focus to how, when, and from whom you order your spare parts. Revisiting and optimizing your reordering process can help you practice better inventory control, improving supplier relationships while preventing costly shortages and stockouts.
For optimal inventory control, determine the very least amount of a given spare part you can have on hand, calculating safety stock and lead time for extra cushion. This calculation is your reorder point—the precise stock level that necessitates replenishing inventory.
Once you’ve established that minimum, update your inventory list accordingly. If you’re using inventory management software like Sortly, set a customized alert so that you’ll be notified when inventory levels for given parts fall below a certain level.
4. Maintain accurate bills of materials
A bill of materials is an itemized list of every single raw material, spare part, and component required to manufacture a finished product. A BOM also articulates how much of each item or part is required, and stipulates secondary goods that must be included with the finished good, such as manuals and packaging.
One of the most important spare parts inventory management best practices is keeping BOMs up to date. That way, you’ll always know exactly what spare parts you need to finish a manufacturing project.
If you’re using inventory management software, you can attach BOMs to an item’s profile for easy access and improved visibility for your whole team. Otherwise, you’ll want to keep them in a clearly-marked, accessible place for quick reference.
5. Forecast demand accurately
By properly forecasting demand, your business can ensure there are enough spare parts to fulfill your customers’ needs. Knowing when to expect surges in demand—plus actually knowing where your spare parts are—can help you avoid costly slowdowns, frustrated customers, and a damaged reputation.
And while proper demand forecasting is essential for just about every business, it’s especially critical for companies like yours, for which a stockout on one small part could create a domino effect of production problems.
6. Train employees on your inventory management system
The ultimate best practice for properly managing spare parts inventory? Complete, effective onboarding of the team you’ll rely on to maintain accurate records. After all, what good is an inventory management system if your employees can’t or won’t use it consistently?
For best results, you’ll want to choose an inventory system that’s simple, customizable, and intuitive. Once you’ve chosen a method that works for your company, train every employee who’ll use the system. Clearly post standard operating procedures, and offer workshops and retraining classes as needed.
Remember, this onboarding doesn’t have to take weeks—or even days. Some inventory apps, including Sortly, have been designed so intuitively that almost all users pick up on the way it works right away.
Experience the simplest inventory management software.
Are you ready to transform how your business does inventory?
About Sortly
Sortly is a top-rated inventory management app perfect for businesses that need to track spare parts. Thanks to Sortly’s powerful features, your team will always know exactly how many nuts, bolts, screws, or nails you’ve got in stock, where they are, and when it’s time to reorder.
Sortly helps you track, manage, and organize your inventory—from any device, in any location. We’re an easy-to-use inventory software that’s perfect for small businesses. Sortly builds inventory tracking seamlessly into your workday so you can save time and money, satisfy your customers, and help your business succeed.
With Sortly, you can track inventory, supplies, parts, tools, assets like equipment and machinery, and anything else that matters to your business. It comes equipped with smart features like barcoding & QR coding, low stock alerts, customizable folders, data-rich reporting, and much more. Best of all, you can update inventory right from your smartphone, whether you’re on the job, in the warehouse, or on the go.
Whether you’re just getting started with small parts inventory management or you’re an expert looking for a more efficient solution, we can transform how your company manages parts inventory—so you can focus on building your business. That’s why over 15,000 businesses globally trust us as their inventory management solution.
Start your two-week free trial of Sortly today.