A crucial part of inventory management is actually keeping up with the inventory on hand. Having a quick, digital system that allows you to quickly scan a product tag to check it in or out is a necessity for most businesses who are managing any level of inventory. This makes it easy to see what you have in stock and what you need to reorder, and can help you track all sales.
When it comes to inventory management, there are two common choices for tracking: barcodes and QR codes, both of which have their own advantages. If you’re deciding between barcodes vs. QR codes for inventory management, you’ll want to weigh the pros and cons of each.
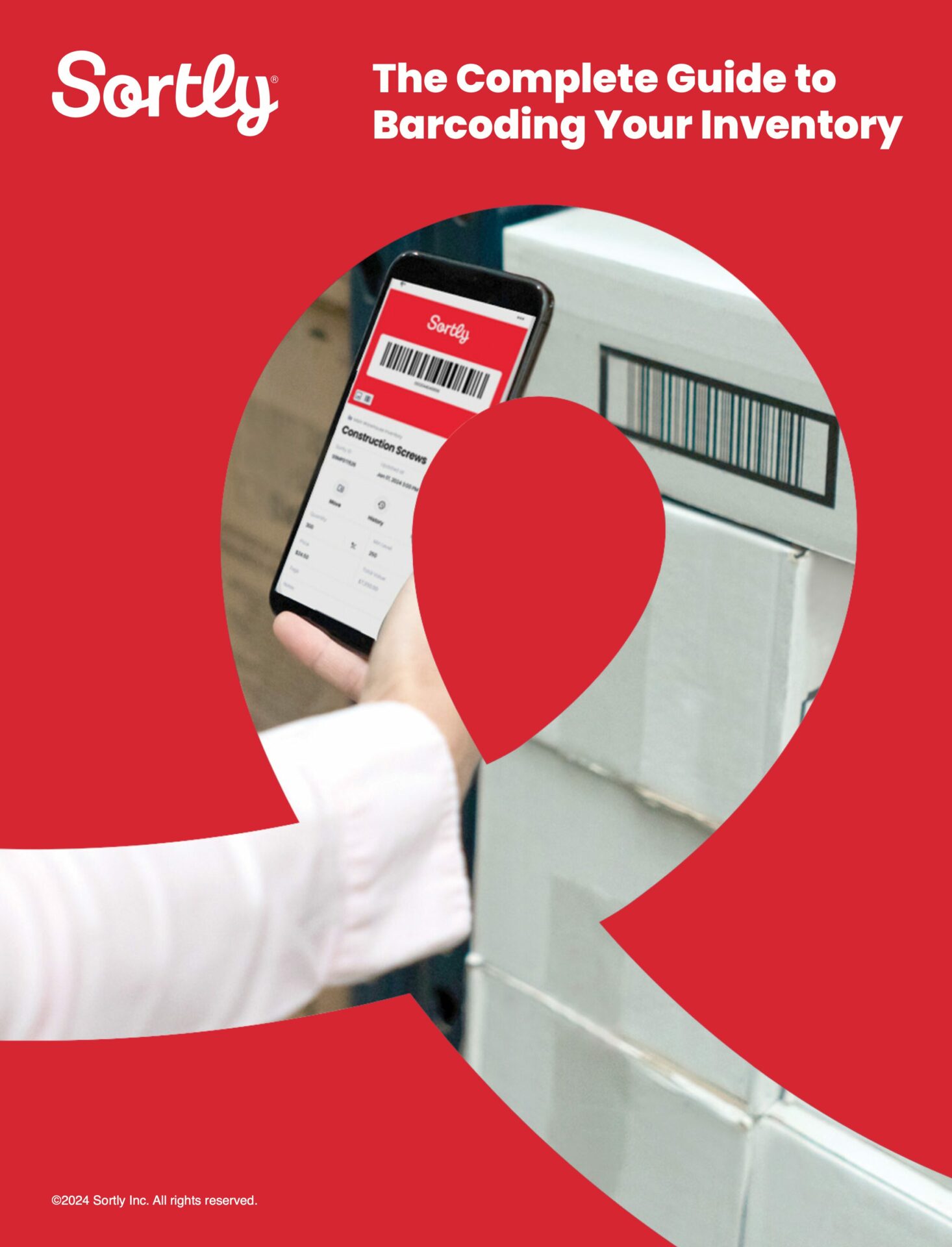
Free Ebook: The Complete Guide to Barcoding Your Inventory
This easy, comprehensive guide will help you:
- Implement a barcode inventory system for your business
- Generate your own unique barcodes
- Practice perpetual inventory control with barcoding
What are barcodes?
Barcodes are small one-dimensional codes that use a series of black bars and white spaces of varying sizes to create unique, individual sequences that are readable by scanners. They’re attached to labels that can be placed on the item, or they can even be printed onto the packing or product itself. which (when read by a barcode scanner) conveys information like the SKU and price of the item.
Barcodes are a commonly-used method to tag and track inventory, which is why you’ve likely seen them show up everything from books to boxes of cereal to exercise equipment.
The pros & cons of barcodes for inventory management
There are clearly plenty of advantages to using barcodes for inventory management; if there weren’t, they wouldn’t be so prevalent amongst small and large businesses alike.
Barcodes are inexpensive to use and print, making them a cost-effective choice for plenty of businesses. They’re also accurate as long as they’re placed on the right product. This makes them preferable to manual systems that are prone to human error. They can speed up your process overall, which can even reduce manual labor and ensure that your inventory management is always up to date.
Barcode systems are also very easy to set up and implement. You can use the barcode scanner built into your smartphone along with barcode generating software like Sortly.
There are, however, a few disadvantages when compared to QR codes.
For starters, they’re one-dimensional. This means they can only be ready horizontally and not vertically. While they can store text-based information about a product like type, size, style, cost, and SKU. They only hold about 20 to 25 characters, depending on the exact type of barcode you’re using.
One-dimensional codes also aren’t as secure as two-dimensional codes, which allow for encryption. If you want high security for the data you’re storing in these codes, barcodes may not be the answer.
Finally, barcodes can be finicky; they typically need to be scanned from specific angles, and some businesses purchase high-contrast scanners to help with this. And if there is an issue with damage, distortion, or an error in printing, there’s a good chance scanners won’t be able to read the information stored.
What are QR codes?
QR codes (which is short for “Quick Response” code) are essentially two-dimensional barcodes that can be read vertically and horizontally. Instead of having a single linear sequence of black lines and white spaces, you’ll get small square codes that use black shapes and white space to convey information.
You’ve likely seen QR codes before on everything from products to retail return systems, or even as a quick way to share your social profiles to get more visits and followers.
Like one-dimensional barcodes, QR codes are ready by machines; these machines can be designated scanners, but users can also pull up apps on their phones to get the information.
Experience the simplest inventory management software.
Are you ready to transform how your business does inventory?
The pros & cons of QR codes for inventory management
Using QR codes for inventory management has a lot of advantages, especially when compared with conventional, one-dimensional barcodes.
Because QR codes can be read vertically and horizontally, they can store significantly more information. While one-dimensional barcodes can only store around 20-25 characters, QR codes can store up to 2,509 numeric characters of 1,520 alpha-numeric characters.
While some businesses may not want or need this level of information, it’s incredibly valuable when you do. You can store product details, website URLs, and plain text in QR codes that you’re attaching to your inventory. If you wanted to track a batch number or where a product was manufactured or imported from, QR codes can help with that.
QR codes are also more secure than one-dimensional barcodes as the information can be encrypted. There’s also less room for error, as they have three levels of error detection built into the code; if something is off, you’ll know.
These codes are also accessible, easily read by the smartphones that we’re all carrying around, and some inventory management tools include QR scanning within their native apps. Since QR codes can be scanned from any angle, they’re even more convenient to use.
The biggest disadvantage of QR codes is what happens when there is an error. If the code is damaged, gets smudged, or somehow distorted, it’ll be unreadable. That being said, simple wear and tear should be a non-issue. To be on the safe side, it’s smart using an app that allows you to reprint barcodes or QR codes so that replacing the labels if needed is a piece of cake.
Barcodes vs. QR codes for inventory management: which is better?
While the answer to this question may seem clear-cut, that’s not always the case.
QR codes are more versatile, and they come with a lot more capabilities than one-dimensional barcodes. If you know that you want to store a ton of information within it (or even think that one day you might), it’s a great choice.
That being said, not all businesses necessarily need or want to store that much information within a tracking code. They just need the product SKU, price, and the ability to check it in or out of their system.
If you’re already set up with a barcode system and it’s working well for you, there’s not really a reason to change over. It can be time-consuming and expensive to convert from one type of code to another, so unless you really want that functionality, there’s nothing wrong with maintaining the status quo.
It’s important to choose a system that works best for your business, so if you’re starting from the ground up, it’s often good to choose the more flexible, feature-filled option. In this case, that would be QR codes. Barcodes and QR codes are both typically highly preferable to manual systems where you’re tracking all of your inventory by hand. They’re both effective and accurate, so both can benefit your business.
Sortly inventory software offers barcode and QR code features
Sortly inventory software allows you to scan barcodes and QR codes right from your smartphone, allowing you to track inventory instantly, from anywhere. You can also generate and print custom barcodes and QR codes for items that don’t already have a barcode. This is great for checking equipment and tools “in and out” as they change hands and location. You can do all of this on a smartphone or tablet, or you can connect third-party scanners to Sortly easily.
Sortly is an inventory management solution that helps you track, manage, and organize your inventory—from any device, in any location. We’re an easy-to-use inventory software that’s perfect for small businesses. Sortly builds inventory tracking seamlessly into your workday so you can save time and money, satisfy your customers, and help your business succeed.
With Sortly, you can track inventory, supplies, parts, tools, assets like equipment and machinery, and anything else that matters to your business. It comes equipped with smart features like barcoding & QR coding, low stock alerts, customizable folders, data-rich reporting, and much more. Best of all, you can update inventory in real time, whether you’re on the job, in the warehouse, or on the go.
Whether you’re just getting started with inventory management or you’re an expert looking for a more efficient solution, we can transform how your company manages inventory—so you can focus on building your business. That’s why over 15,000 businesses globally trust us as their inventory management solution.
Start your two-week free trial of Sortly today.
Download Sortly free on iOS and Android: