If your business uses raw materials to manufacture finished goods, then chances are it’s already developed a raw materials inventory management strategy to keep track of this particular type of inventory. That’s because raw materials are essential to many businesses’ production schedules and because these products are often expensive, difficult to store, and kept across multiple locations or job sites.
In this article, we’ll walk you through how to calculate raw materials inventory, providing key formulas for both beginning raw materials and ending raw materials inventory.
What are raw materials?
Many businesses agree that raw materials can be particularly difficult to store, manage, and track. From construction companies to manufacturing plants, learning to properly store and account for raw materials can help your business save time, money, and stress at once.
On the same note, sitting down and accounting for the value of your raw materials at the beginning and end of each financial period can help your business practice better inventory control, prepare more accurate balance sheets, and forecast demand for the future.
Related: How to Track Raw Materials
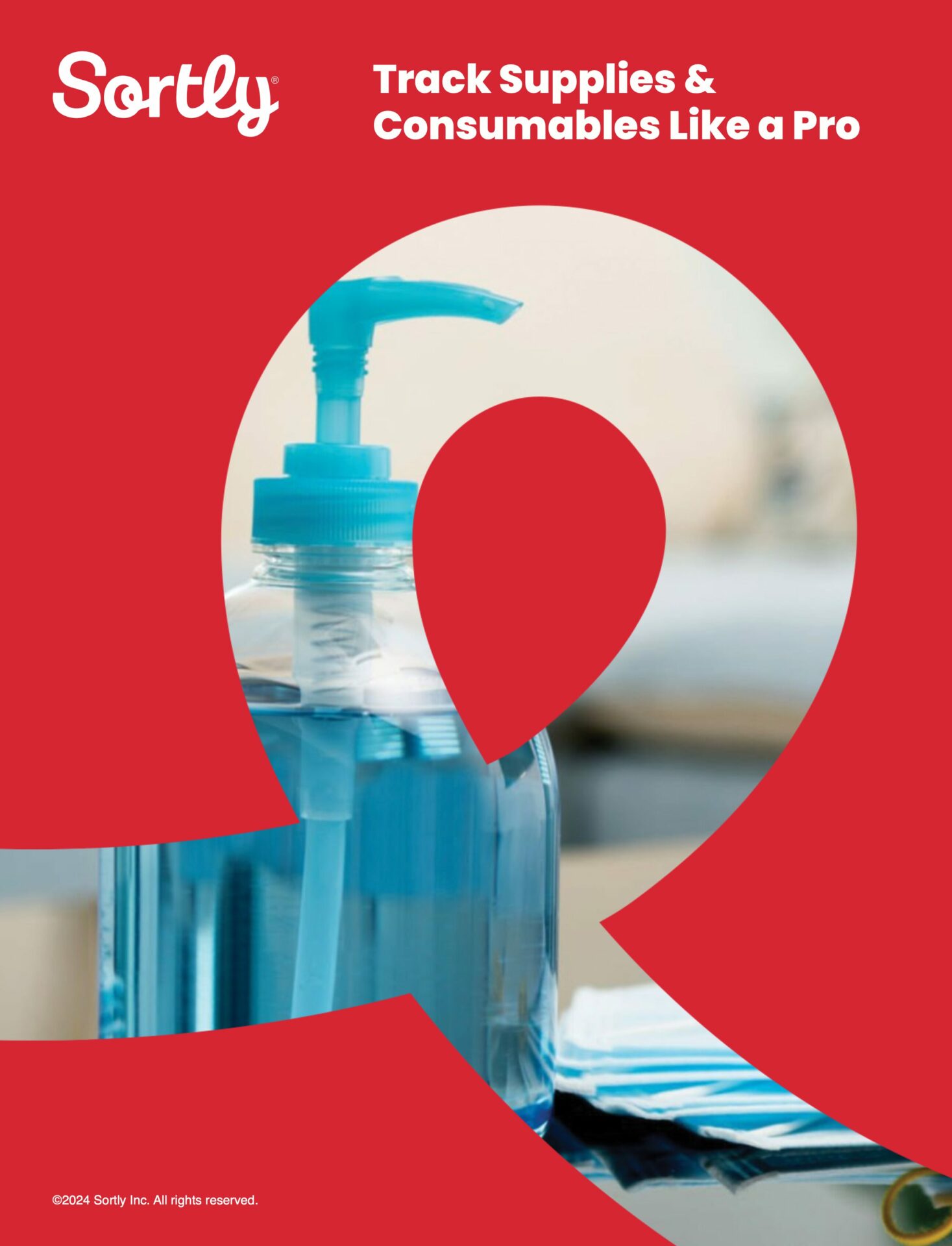
Free Ebook: Track Supplies & Consumables Like a Pro
This easy, comprehensive guide can help you:
- Create an inventory list for supplies and consumables
- Automate reordering with alerts and expiration reminders
- Perform inventory audits for consumable inventory
How to calculate raw materials inventory
Want to calculate raw materials used? You’ll need the following information:
- Your company’s beginning raw materials inventory—in other words, the amount of inventory at the opening of a given period
- Purchased raw materials—raw materials your business has purchased since the opening of that same period
- Costs of Goods Sold (COGS)—the direct costs of the raw materials associated with producing the inventory you’ve sold
Beginning raw materials inventory
Keep in mind that your beginning raw materials inventory for the next period is simply your ending raw materials inventory for the previous one. You can calculate it using the beginning inventory formula for only your raw materials.
Beginning Raw Materials Inventory = (COGS + Ending Raw Materials Inventory) – Raw Materials Inventory Purchases
For example, imagine a manufacturer produces lanterns using iron. Iron costs $50 a unit, and the business ended the last accounting period with 1,000 units in stock. Over the last period, the manufacturer also sold 200 lanterns and purchased an additional 250 units of iron.
- Ending Raw Materials Inventory = 1,000 units at $50/unit ($50,000)
- Purchased New Materials = 250 units at $50/unit ($12,500)
- COGS = 200 units at $50/unit ($10,000)
→ Beginning Raw Materials Inventory = ($10,000 + $50,000) – $12,500
→ Beginning Raw Materials Inventory = $47,500
The lantern manufacturer’s beginning raw materials inventory for the first day of its new accounting period is valued at $47,500. As noted, this is also the business’s ending raw materials inventory for the previous accounting period.
Ending raw materials inventory
Wondering how to calculate ending raw materials inventory? The official formula for calculating ending raw materials inventory is as follows:
Ending Raw Materials Inventory = (Raw Materials Inventory Purchases + Beginning Raw Materials Inventory) – COGS
Say a lightbulb manufacturer begins a new accounting period with 1,000 units of glass on hand. During that accounting period, they purchase another 200 units of glass and sell 700 lightbulbs, all for $.50 per unit.
- Beginning Raw Materials Inventory = 1,000 units at $.50/unit ($500)
- Purchased New Materials = 200 units at $.50/unit ($100)
- COGS = 700 units at $.50/unit ($350)
→ Ending Raw Materials Inventory = ($100 + $500) – $350
→ Ending Raw Materials Inventory = $250
The lightbulb manufacturer ends its current accounting period with $250 worth of raw materials inventory. Remember that this will become the business’s beginning inventory for the next accounting period.
About Sortly
Sortly is an inventory management solution that helps you track, manage, and organize your inventory—from any device, in any location. We’re an easy-to-use inventory software that’s perfect for small businesses. Sortly builds inventory tracking seamlessly into your workday so you can save time and money, satisfy your customers, and help your business succeed.
With Sortly, you can track inventory, supplies, parts, tools, assets like equipment and machinery, and anything else that matters to your business. It comes equipped with smart features like barcoding & QR coding, low stock alerts, customizable folders, data-rich reporting, and much more. Best of all, you can update inventory right from your smartphone, whether you’re on the job, in the warehouse, or on the go.
Whether you’re just getting started with inventory management or you’re an expert looking for a more efficient solution, we can transform how your company manages inventory—so you can focus on building your business. That’s why over 15,000 businesses globally trust us as their inventory management solution.
Start your two-week free trial of Sortly today.