Every construction company needs to find a place to store construction materials—and then figure out the smartest, most efficient way to track them. And whether your company builds houses all over the country or helps renovate offices in just one part of town, properly storing construction materials is essential.
In this article, we’ll dive into how to store construction materials, exploring everything from construction site storage best practices to choosing the right inventory system to streamline your strategy.
What are construction materials?
Construction materials are any material or good that is utilized for construction—at any time in the construction process. These materials, which are often raw materials, may include paint and printer, cement, stone, bricks, tile, drywall, and flooring like carpet, hardwood, or vinyl. Construction materials can also be finished goods, like cabinet handles and light fixtures, if the construction company has been tasked with installing these items.
Where do you store construction materials?
Construction professionals store materials in a variety of places, including right on the job site, in company vehicles, or in a storage facility or warehouse. Deciding the best place to store construction materials isn’t always a simple choice. Here are a few of the pros and cons to each storage location.
Storing construction materials on a job site
There’s often no easier, more convenient solution to your construction company’s storage woes than construction site storage. After all, everything your team needs to get the job done is right there, waiting for them.
However, there are important downsides, too. Construction sites can be hard to secure, and materials can’t always be kept in tip-top condition if they’re overexposed to the elements. Plus, this inventory can sometimes be difficult to track if your on-the-job employees aren’t trained to manage inventory.
Storing construction materials in company vehicles
Another option is to store at least some construction materials in your company trucks or cars. While this may not be a solution for large quantities of materials, there are certain goods for which vehicular storage makes sense. It can also keep valuables more secure, as long as they are not left on the job site overnight.
The primary downside is simply size: a vehicle cannot fit the often massive materials used for construction. In general, company trucks should store tools and small equipment rather than materials.
Related: How to Track Your Tools
Storing construction materials in a storage facility or warehouse
If you are unable to safely, properly store materials on your job site, your best bet is to keep construction materials in a storage facility or warehouse where they are readily accessible. This could be a storage unit, a warehouse, or even a rented space that’s close to one or more of your job sites.
Whatever you decide, you’ll want to consider investing in the right security and surveillance systems to keep your raw materials safe—especially high-value ones, such as copper wire.
Related: How to Reduce Inventory Shrinkage
How to store construction materials
Storing construction materials varies quite a bit depending on what you need to store and where you need to store it. But these best practices can help your team figure out your construction material storage strategy.
1. Keep similar materials together
One of the easiest ways to keep your construction inventory organized is by keeping similar items together. What’s more, many construction materials have particular storage requirements, so by storing like items together, you’ll also protect those investments.
Lumber
Lumber, for example, is extremely porous–it quickly absorbs water that can damage or even destroy the wood. You’ll want to store lumber horizontally, with plenty of air between the pieces to allow for better circulation. You’ll also want to create a base using bricks or cinder blocks so your lumber is never flush against the floor, where moisture can easily build.
If you choose vertical storage to save space, keep lumber raised and consider buying or building a vertical storage rack to prevent bowing.
Tile
Tile is fairly easy to store and not nearly as vulnerable as wood. Find a cool, dry place to store tile, and consider stacking the tiles upright to reduce the risk of breakage.
Cement
Cement requires absolutely no exposure to moisture until the time has come to prepare it. That means outdoor storage is practically forbidden—even if you’re smart about it, and even if you use a tarp. Instead, find a dry, well-ventilated indoor space where you can keep cement at least a couple feet away from any walls and floors.
Use tarps, of course, but only as a last resort to protect your cement from disaster.
Bricks
Brick storage is relatively straightforward, and you can store them inside or out. If you do choose to store them where they’ll be exposed to weather, place a tarp beneath and above your brick materials to protect them from unnecessary water exposure.
Paint
Paint should be perfectly sealed and kept in a cool place—but not too cool. The ideal storage temperature for paint is between 50 and 75 degrees. Smaller paint containers tend to allow less air in, but you can also use a layer of plastic wrap over paint in a larger paint can to keep extra air out.
2. Decide where you’ll store your materials
Now that you know what to consider when selecting your storage spaces, it’s time to decide exactly where you’ll keep your construction materials. Assess all available locations for storage, mapping them out against the locations that matter: where your office is, where your job sites are, where your employees live.
You’ll also want to consider the complexities of your service area. How’s the weather? Is traffic bad? How secure are your construction sites? Are you able to keep materials behind a locked fence? Once you know those answers, consider your storage budget. Questions like these can help you determine where you should store materials to maximize efficiencies and reduce inventory shrinkage.
It’s likely that you will end up storing your materials in more than one location. Sortly’s inventory management software allows you to track inventory in multiple locations easily—simply update the inventory location with the click of a button.
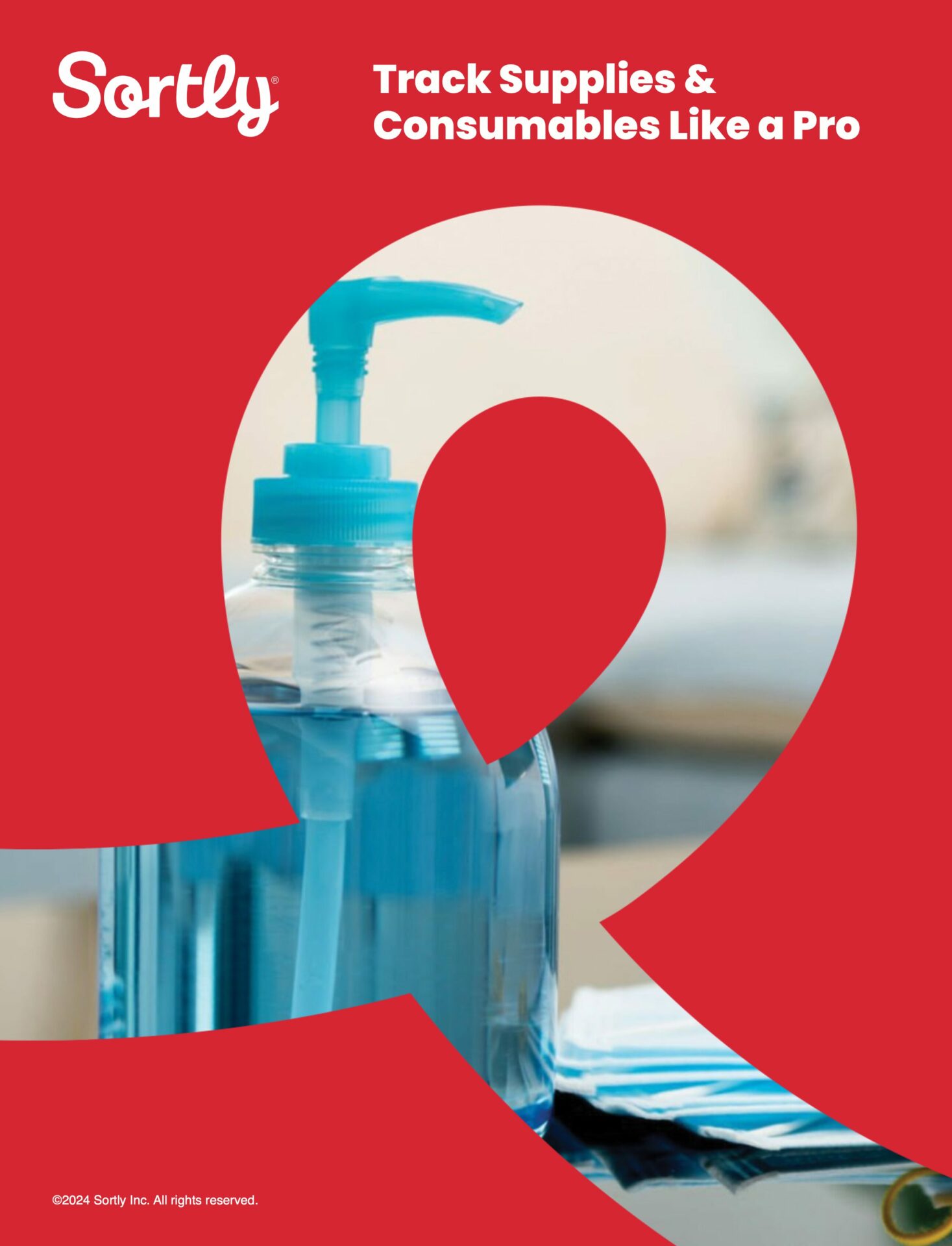
Free Ebook: Track Supplies & Consumables Like a Pro
This easy, comprehensive guide can help you:
- Create an inventory list for supplies and consumables
- Automate reordering with alerts and expiration reminders
- Perform inventory audits for consumable inventory
3. Create a security plan
No matter where or how you decide to store your construction materials, you’ll want to iron out a plan to keep that inventory safe and secure. Whether that’s building some kind of tool crib that also leaves space for high-value items, implementing an airtight inventory management system, or investing in surveillance cameras for your warehouse or storage unit.
4. Choose an inventory system that helps you stay organized
Whether your company is working on one project or a hundred, keeping track of all your construction inventory, materials, and supplies is not a simple task. Choosing the right inventory management system can help you stay organized day in and day out, even as new materials arrive and old ones are used up.
The right inventory management system will also help you understand exactly what materials are where at any given time, making it easy for your employees to grab the right inventory before they go to a job site or start working on a complicated project.
Inventory management software, for example, can help you see your inventory across multiple locations, quickly check items in and out using barcodes and QR codes, and even keep track of project costs by creating a clear history of what products have been used at what job site.
Related: How Bilo Heating & Plumbing Uses Sortly to Stay On Top Of Supplies, Materials
About Sortly
Experience the simplest inventory management software.
Are you ready to transform how your business does inventory?
Efficient inventory tracking is a must for construction companies and service providers. If your business would benefit from improved inventory management, consider switching to Sortly today. Sortly lets you organize, track, and manage your inventory—from any device, in any location. Our easy-to-use mobile app lets you and your team update inventory on the job, scan barcodes from your smartphone, set low stock alerts to remind you to re-order, and more. That means you can work more efficiently, plan for jobs better, and serve your customers to their highest satisfaction.
Join the over 15,000 professionals who trust Sortly as their inventory management solution and start your free 14-day trial.