When tracking the maintenance of a business’s equipment, many organizations implement a barcode or QR code system to keep tabs on these assets and ensure all equipment maintenance is properly archived and scheduled. In this article, we will focus on how to use QR codes for equipment maintenance.
The following three-step process is a simple and customizable approach to creating a QR code system to help your business keep track of equipment maintenance. While many organizations will fold their equipment maintenance tracking strategy into a broader, QR code-powered inventory management strategy, companies that do not wish to update their entire inventory tracking strategy can still utilize the following steps for tracking equipment maintenance only.
1. Select a QR code system
To get started with a barcode or QR code system for equipment maintenance tracking, you’ll need to select an inventory management system that easily connects QR codes to equipment. There are a variety of inventory software solutions and apps capable of doing this. When searching for a solution, many businesses prioritize apps and software that:
- Are simple and intuitive enough to be used by every employee, including those who are not tech-savvy.
- Offer a free trial.
- Are scalable and customizable.
- Do not rely on expensive external equipment, such as QR code scanners and specialty printers.
- Allow employees to “scan on the go” using existing devices such as smartphones or tablets.
- Enable users to generate custom QR codes and print them on everyday label paper using standard printers.
- Allow users to utilize either manufacturer’s barcodes or QR codes and generate new ones.
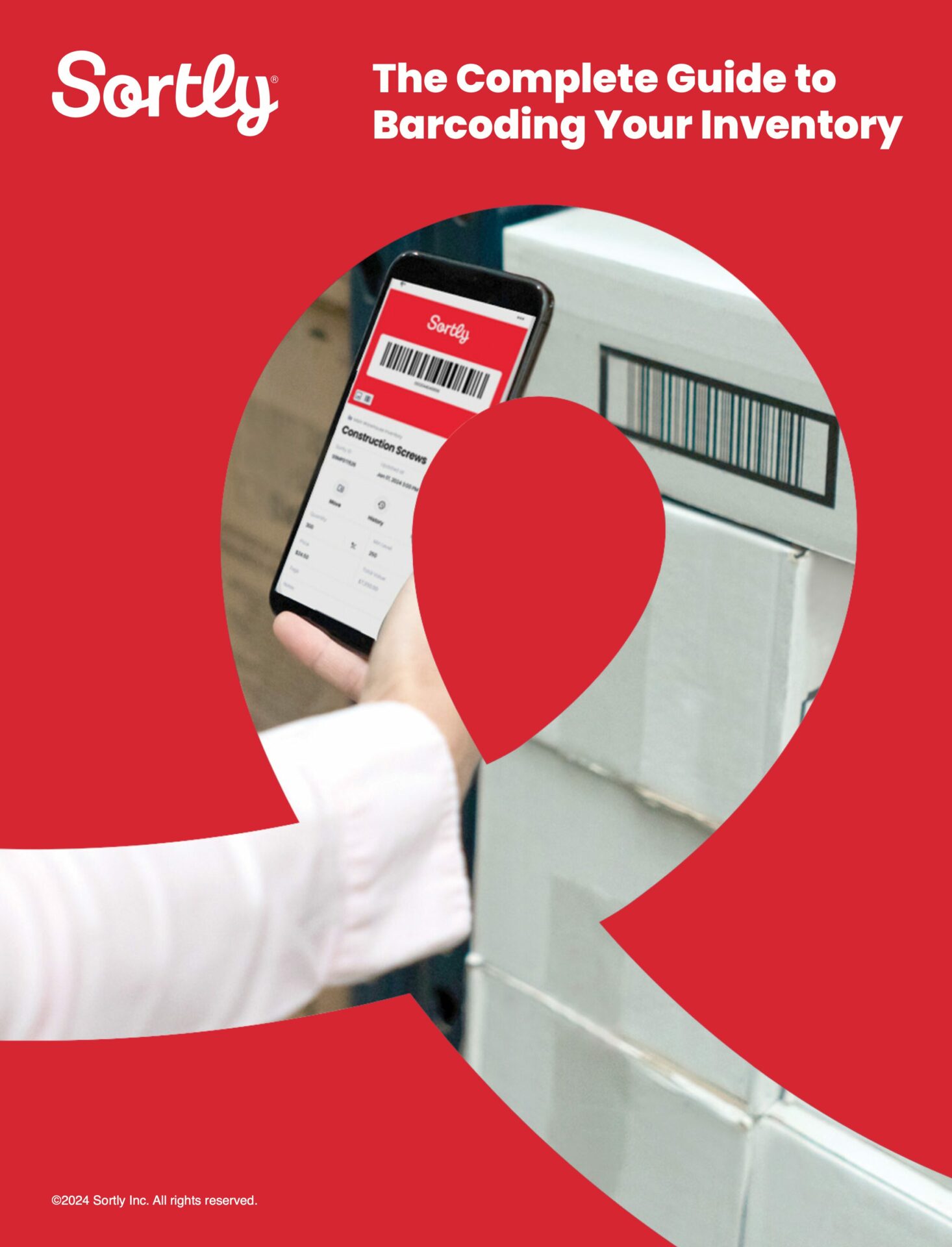
Free Ebook: The Complete Guide to Barcoding Your Inventory
This easy, comprehensive guide will help you:
- Implement a barcode inventory system for your business
- Generate your own unique barcodes
- Practice perpetual inventory control with barcoding
2. Organize all inventory with QR codes
Once you have selected a QR code system for your equipment maintenance, you must organize all your inventory data within the software. If you have selected intuitive inventory management software, this should be relatively simple.
First, create an equipment list of all the equipment you’ll need to track. You can create this list on a sheet of paper, using a spreadsheet, or directly in your app. You’ll want to enter all key details about each piece of equipment, including vendor, location, value, and condition. If you’re using a solution like Sortly, you’ll also be able to add high-resolution photos and any crucial attachments, including manuals, warranties, and notes and reports from previous service appointments.
You’ll also be able to include customized alerts and reminders about equipment maintenance. These alerts and reminders can help you remember to schedule upcoming planned maintenance. You can also store previous maintenance schedules, notes, and histories as attachments or text within each item’s profile.
Once all this information is in the system, you’ll want to connect each piece of equipment with its QR code. If the equipment already came with a QR code or barcode provided by the manufacturer, you can scan that code to get started. If there is no QR code, you can use a QR code generator such as Sortly to rapidly create a custom label for the item.
Once all item profiles are complete and synced with QR codes, your team will not only automatically be reminded about upcoming maintenance dates or warranty end dates but can also rapidly scan any QR code at any time to pull up details about a piece of equipment. At once, your team will have access to all the information about an item’s maintenance history and upcoming appointments, all in one place.
This benefits your team and any vendors who need to perform work on the item and have questions about its history. In a blink, you can pull up information about the item’s repair history or performance history without sifting through thousands of emails or rifling through a too-full filing cabinet.
What’s more, equipment tracking software makes it easy for your accountant to claim depreciation on tracked equipment when that software automatically creates maintenance histories that show a decline in condition and value over time.
Related: Types of Equipment Maintenance and Why They Matter
3. Standardize your equipment maintenance process in an SOP
An SOP for equipment maintenance, or a standard operating procedure, is an official document that articulates precisely how your business handles equipment maintenance and tracking. Whatever QR code system your company decides to implement, the precise details of that strategy should be recorded in this document.
Specifically, the SOP should clarify:
- How equipment is physically organized and stored within your business.
- What information about every piece of equipment should be cataloged in the inventory software and how, including details on attachments and photos.
- How equipment maintenance and equipment itself will be audited.
- How equipment maintenance is scheduled, which vendors your business works with, and how to retrieve information about maintenance during service.
Many businesses implement an equipment QR code system that matches the rest of their organization’s inventory management strategy. This enables the company to implement a single inventory management strategy that utilizes QR codes to streamline and simplify inventory management across the board.
This tends to improve adherence since only one standard operating procedure applies to virtually all inventory management practices, including equipment tracking. The result is a more thorough and robust equipment management strategy that boosts profitability and productivity in both the short and long term.
About Sortly
Sortly is an inventory management solution that helps you track, manage, and organize your inventory from any device, in any location. We’re an easy-to-use inventory software that’s perfect for large or small businesses. Sortly builds inventory tracking seamlessly into your workday so you can save time and money, satisfy your customers, and help your business succeed.
With Sortly, you can track inventory, supplies, parts, tools, assets like equipment and machinery, and anything else that matters to your business. It comes equipped with smart features like barcoding & QR coding, low stock alerts, customizable folders, data-rich reporting, and much more. Best of all, you can update inventory right from your smartphone, whether you’re on the job, in the warehouse, or on the go.
Whether you’re just getting started with inventory management or you’re an expert looking for a more efficient solution, we can transform how your company manages inventory—so you can focus on building your business. That’s why over 15,000 businesses globally trust us as their inventory management solution.
Start your two-week free trial of Sortly today.