Just about every business needs to keep track of inventory—but there are many ways to do it: by hand, via spreadsheet, using an inventory app. So, how does your unique business decide which inventory management system is suitable for you—and how do you decide between a manual vs. automated inventory system?
In this guide, we’ll define both manual and automated systems, then review the advantages and disadvantages of both. We’ll also explore how the right inventory management software can help your business stay organized whether you choose a manual system, an automated system, or a combination of the two.
What is a manual inventory system?
Alternatively, your company may not even track inventory perpetually. Instead, your business will rely on physical inventory counts to determine what’s on hand, what’s running low, and what needs to be reordered. If your team doesn’t know what’s on hand until they walk into a storage room and physically count it, it’s considered physical manual inventory management.
These physical inventory counts could happen as needed or at regularly scheduled times. (No matter what kind of inventory system you use, your business will probably conduct some form of end-of-year inventory count, too.)
It’s also possible—but tricky—for a business to conduct perpetual manual inventory. If your team constantly knows what’s on hand in real time, but they’re manually updating an inventory sheet every time an item comes or goes, then it’s considered a perpetual manual inventory management system.
Related: What Is the Difference Between Perpetual Inventory and Physical Inventory?
What is an automated inventory system?
An automated inventory system also allows companies to stay several steps ahead of inventory shortages and stockouts. That’s because an automated inventory system reveals exactly what’s in stock at a given moment. Plus, the best automated inventory management software will alert the right users when a certain item’s stock levels are dwindling, or an item is approaching expiration or warranty end.
Automated inventory control systems also use barcodes and QR codes to help employees quickly and accurately update inventory data.
For example, when a case of windshield wiper blades arrives at an autobody shop, employees can quickly “check in” the items by scanning the barcode on the box, then adding the new quantity to the existing stock. Apps like Sortly make this even easier by enabling barcode and QR code scanning using the camera from a smartphone or tablet.
Manual vs. automated inventory system
There are many advantages to an automated inventory management system, but ultimately the system that’s right for you depends on your business’s unique features and priorities. Here are some of the most significant pros and cons to both inventory system types:
Benefits of a manual inventory system
Manual inventory systems can be a good choice for very small businesses that do not carry much inventory. For example, if your company stocks just a few dozen products in one location, it can be easy to track inventory by hand as it comes and goes.
And if your team falls behind on keeping inventory, that may not affect your business too much. After all, your inventory is nearby—and conducting a physical inventory count only takes a few minutes.
A manual inventory system is also inexpensive—you can set one up on a sheet of paper or an inventory spreadsheet for free.
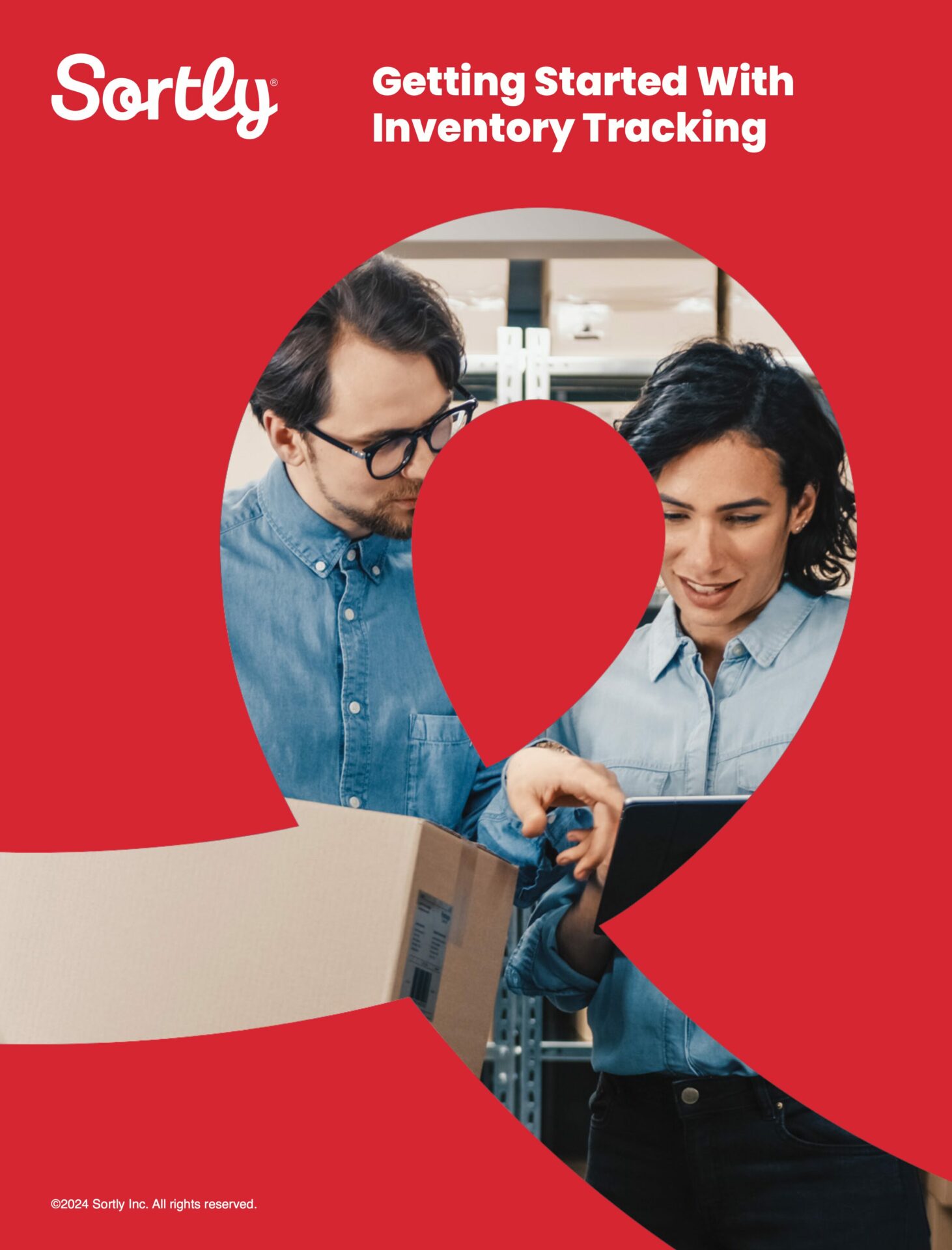
Free Ebook: Getting Started With Inventory Tracking
This easy, comprehensive guide will help you:
- Determine your business's inventory levels and needs
- Organize your inventory for optimal tracking
- Follow tried-and-true best practices for inventory management
Drawbacks of manual inventory system
Unfortunately, a manual inventory system is quite vulnerable to human error. For example, a few jumbled numbers or data-entry errors can cause costly inventory shortages or stockouts that could affect your business’s bottom line.
Furthermore, a manual inventory system can quickly become unmanageable. That’s because as your business grows, you’ll have more and more inventory to manage. Handling all those items manually can take up way too much of your and your employees’ valuable time—and eventually become so time-consuming that inventory tracking could slip through the cracks.
And even if you and your team maintain a manual inventory system as your business grows, time is a valuable resource. If it’s taking hours to track inventory every day, that could be time and money better spent on marketing, hiring, or other business improvements.
Benefits of automated inventory system
There are many benefits to using an automated inventory system.
Most notably, you and your team will always have an up-to-date, accurate picture of what your shelves, stockrooms, and warehouses look like. Knowing what you’ve got in stock allows your company to practice airtight inventory control while easily satisfying customer demand.
And if you use an automatic inventory management system that allows you to set customized alerts, you also won’t have to worry about stockouts, shortages, or items expiring or falling out of warranty. This won’t just save your company from a major headache; it’ll keep your company profitable, productive, and completely aware of what’s in stock, what’s running low, and what needs to be used up fast.
Since an automated inventory system stores data on inventory management software, you’ll also have access to tons of useful information about your inventory and inventory history. You can use customized reports and insightful data to forecast demand, schedule maintenance, generate an inventory list, and conduct an inventory or asset audit.
Drawbacks of automated inventory system
There aren’t many drawbacks to an automated, modern inventory system. However, some systems are too complex and confusing for employees to maintain. That’s one of the reasons Sortly was created—it’s intuitive, simple, and doesn’t require in-depth training.
Choose an automated inventory system that’s intuitive and easy to use. Ideally, the inventory app or software you select should be simple, customizable, and make sense to even the least tech-savvy employees at your business.
Experience the simplest inventory management software.
Are you ready to transform how your business does inventory?
Inventory management software for keeping automated inventory
To keep automated inventory, you’ll need to select inventory management software that allows you to easily update when items are bought, sold, moved from location to location, or checked in and out.
Even if you want to keep track of inventory manually for now, updating your inventory counts in an inventory app like Sortly can be quite beneficial. After all, you’ll be able to tap into a host of features, including customized reports, alerts, adding photos and attachments to your item profiles, and more. Then, once you’ve counted your inventory for the day, week, or month, you can simply update your inventory counts right in the app.
If you decide you’re ready to try a perpetual, truly automatic inventory management system, you’ll already have all your inventory information in one place. And all the features you need to make the switch will be waiting for you: a barcode and QR code scanner, the ability to create customized barcodes and QR codes for unlabeled stock, the ability to check items in and out, and customizable alerts.
About Sortly
Sortly is an inventory management solution that helps you track, manage, and organize your inventory—from any device, in any location. We’re an easy-to-use inventory software that’s perfect for small businesses. Sortly builds inventory tracking seamlessly into your workday so you can save time and money, satisfy your customers, and help your business succeed.
With Sortly, you can track inventory, supplies, parts, tools, assets like equipment and machinery, and anything else that matters to your business. It comes equipped with smart features like barcoding & QR coding, low stock alerts, customizable folders, data-rich reporting, and much more. Best of all, you can update inventory right from your smartphone, whether you’re on the job, in the warehouse, or on the go.
Whether you’re just getting started with inventory management or you’re an expert looking for a more efficient solution, we can transform how your company manages inventory—so you can focus on building your business. That’s why over 15,000 businesses globally trust us as their inventory management solution.
Start your two-week free trial of Sortly today.