Managing inventory effectively is a critical aspect of any construction company’s success. Ensuring the right supplies, materials, equipment, and machinery are on site when required ensures projects are finished on time, as designed, and at budget.
This article will explore seven best practices construction companies use to optimize inventory management.
What is inventory management for construction?
In construction, inventory management refers to tracking and controlling the supplies, materials, and assets required to execute construction. Supplies and materials often include raw materials like lumber and steel and hundreds of special tools, and assets may include extremely high-value equipment like tractors and cranes.
Regardless of what your construction company keeps on hand, optimizing how you procure, store, track, and audit this inventory can ensure projects are completed on time and within budget. Moreover, optimizing construction inventory management and inventory control reduces waste, improves sustainability, prevents supply shortages and stockouts, and enhances productivity by ensuring the right materials and equipment are in the right place at the right time.
Construction companies practicing inventory management typically use one of three systems: manual inventory management (pen-and-paper), spreadsheet inventory management, or inventory management software.
The following best practices are some of the most critical aspects of an optimized inventory management strategy. They’re practiced by construction companies of every shape and size, from small businesses serving just a few customers to international operations executing projects all over the world.
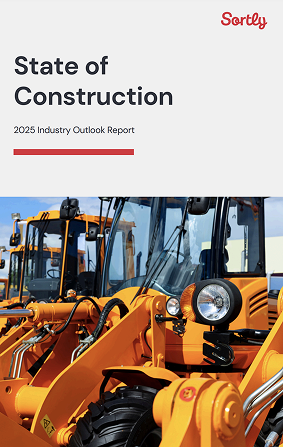
Download Sortly's 2025 State of Construction Report
Download our free 2025 construction industry report for must-know insights on:
- 2025 outlook for commercial, residential, and industrial construction.
- Top construction industry challenges.
- Technology’s role in construction.
1. Perform a comprehensive inventory analysis
Also known as an inventory audit, a comprehensive inventory analysis allows construction team members to thoroughly examine inventory, determine precisely what they have on hand across all storage locations, and categorize materials and equipment accordingly.
More specifically, comprehensive inventory analysis is a multi-step process that categorizes and classifies all inventory by type, usage, importance, and ideal storage condition. This classification creates an inventory hierarchy that identifies what inventory is most essential to which projects and to the company’s overall profit.
Many construction companies utilize some form of ABC classification to determine their most important and valuable inventory. This allows stakeholders to focus their most controlled inventory management efforts on the items that matter most.
This audit should also verify inventory quantities across every location. While this may be tedious if performed manually, recording exactly what inventory is on hand is essential to an efficient and organized inventory management strategy. Employees should compare the counts on hand to documented quantities and then identify and report discrepancies.
Finally, as employees physically verify inventory, they should update their manual, spreadsheet, or software inventory system. Employees should note the following:
- Confirmed quantities on hand versus amounts reported
- The precise location of the inventory
- Whether inventory appears damaged
- Whether stock appears to be at risk of shrinkage or obsolescence
- Whether asset conditions have changed
Inventory audit best practices include:
- Utilizing digital tools and software, if available, to keep better track of inventory between audits.
- Regularly updating inventory records to reflect current stock levels.
- Training employees to count inventory, analyze its condition, and use a QR code system to speed up these processes.
Since audits can be time-consuming, conducting as many inventory-related tasks as possible during this time will help your business get the most ROI from the process. Businesses that have adopted a barcode or QR code inventory system can perform inventory verification in a fraction of the time since items can be scanned and validated in real time.
2. Implement the right technology solutions
Many construction companies are adopting more modern inventory management solutions to maintain accurate inventory records with less effort. Integrating technology solutions, such as barcode scanners and inventory software, can rapidly streamline inventory management and enable real-time, perpetual tracking of raw materials, construction supplies, and machinery. This reduces ordering mistakes that add up quickly and ensures that inventory and assets are always on the right job site before the workday begins.
Consider a construction company with projects underway across the entire state. Chances are this business stores material at headquarters, job sites, storage facilities, and on the company’s fleet of trucks. By implementing a mobile inventory management app, field teams can scan QR codes on supplies and materials and input usage data right away. They can also update the location of machinery as it moves from one site to another. This allows on-site project managers and off-site stakeholders to clearly understand inventory levels at any job site at any time—and gives them ample time to move supplies, materials, and assets around before it slows down progress.
Inventory management apps such as Sortly also notify the right people when the quantity of certain items drops below a given threshold. When these customized low-stock alerts are aligned with vendors’ lead times, construction companies can confidently place complete orders at exactly the right time. This helps reduce the risk of materials shortages that cause costly schedule delays and eliminates the significant labor charges incurred when employees must drive across the county to search for supplies that should have already been on site.
This easy, comprehensive guide will help you:
Free Ebook: Getting Started With Inventory Tracking
3. Implement just-in-time principles
Just-in-time inventory minimizes inventory kept on hand by aligning critical inventory deliveries with project schedules. To achieve JIT, your company must establish relationships with reliable suppliers that deliver without issue consistently and as promised. This allows your business to front as little cash as possible for inventory on hand while mitigating the risks associated with over and understocking.
For example, imagine a national builder of retail stores for a coffee company that relies on a shortlist of trusted vendors to supply tile and flooring for their shops. This corporation may implement JIT so the right materials arrive at the right stores at just the right time. As a result, cash is only spent on materials as soon as needed, giving the corporation more financial flexibility in other areas. It also reduces the resource burn of storing and securing materials before they’re required to complete a task.
If you want to implement JIT principles into your construction company’s inventory strategy, you should:
- Determine which materials are critical to your jobs, then create a schedule for inventory delivery based on project timelines.
- Develop relationships with suppliers that consistently deliver materials on time and in good shape.
- Mitigate risk by drafting contingency plans that address potential delivery delays.
4. Forecast demand
Demand forecasting is the process of predicting supply, material, and equipment requirements based on your company’s historical data, as well as an analysis of market trends and project schedules over the next period. This data-driven approach to inventory management helps construction companies make more intelligent decisions about procuring and allocating resources.
For more insight into market trends, construction stakeholders should chat with their most trusted suppliers about vulnerabilities in the supply chain. Chances are your vendors know what other construction companies are ordering and how supply and demand for certain products may fluctuate over the next while. These insights can help you secure products that may later become difficult to stock or even allow you to purchase them at a lower rate before demand surges.
Demand forecasting best practices include:
- Consistently collecting and analyzing data on how your business is using inventory.
- Leveraging technology or other knowledge that considers variable factors like construction outlook and seasonality.
- Constantly reviewing and adjusting forecasts as projects evolve and new requirements come to light.
5. Collaborate cross-functionally
Construction requires various companies and teams to work together to execute a job, so it’s no surprise that optimizing collaboration and communication between stakeholders is vital. Open communication with all teams ensures that materials and equipment are available when needed, especially if a project is prone to last-minute changes or rework.
Suppose a construction company works with an owner and an architect who are constantly requesting project changes. In that case, the construction company should schedule daily chats with stakeholders about the next steps. This allows the construction company to process change orders rapidly and urgently place material requests with trusted, speedy vendors.
Best practices for collaboration and communication with other stakeholders include:
- Maintaining solid relationships with suppliers, field teams, owners, and more.
- Sharing project schedules and updates with vendors to enable timely material delivery.
- Ensuring inventory databases are always updated so materials can be rapidly and confidently moved between sites when needed.
6. Improve inventory management processes
During your initial inventory audit or any other time, you may find vulnerabilities in your supply, material, and equipment management processes that need attention. This is expected during an audit—and is proof of a thorough investigation.
For example, if a business discovers that its copper inventory does not match the expected quantities on hand, new security measures should be implemented. These may include leasing space at a secure storage facility, keeping these high-value raw materials under lock and key, or adding closed-circuit security cameras to an already secure storage area.
Remember that even the best inventory management systems require updating as businesses grow. Regardless of the success of your inventory management strategy, your company should regularly assess all processes, gather feedback from employees, identify vulnerabilities, and tweak the inventory management process to ensure the system is working as smoothly as possible.
Best practices for ongoing inventory management optimization include:
- Using an inventory software system like Sortly to track, organize, and manage inventory easily and improve crucial visibility.
- Consider barcoding your inventory to save time and ensure even greater real-time accuracy across all the items you track.
- Updating inventory management systems and standard operating procedures to reflect current best practices.
About Sortly
Sortly is an inventory management solution that helps you track, manage, and organize your inventory from any device, in any location. We’re an easy-to-use inventory software that’s perfect for construction businesses of all sizes. Sortly builds inventory tracking seamlessly into your workday so you can save time and money, satisfy your customers, and help your business succeed.
With Sortly, you can track construction inventory like supplies, parts, tools, equipment, and anything else that matters to your construction business. It comes equipped with smart features like barcoding & QR coding, low stock alerts, customizable folders, data-rich reporting, and much more. Best of all, you can update inventory right from your smartphone, whether you’re on the job, in the warehouse, or on the go.
Whether you’re just getting started with inventory management or you’re an expert looking for a more efficient solution, we can transform how your company manages inventory—so you can focus on building your business. That’s why over 15,000 businesses globally trust us as their inventory management solution.
Start your two-week free trial of Sortly today.