MRO inventory refers to the inventory kept on hand for maintenance, repair, and operations. In other words, it is the category of supplies and materials a business needs for production that do not end up becoming part of a manufactured end product. As a result, MRO inventory optimization is often an afterthought for even the most organized businesses. After all, it’s not directly revenue-generating.
This article will touch on how to optimize MRO inventory so that your business can remain just as productive while tying up fewer resources on MRO inventory.
What is MRO inventory optimization?
Related: What is MRO inventory?
Why is optimizing MRO inventory important for many businesses?
Many businesses optimize their inventory and asset management strategies. After all, traditional inventory and assets are neatly connected to an organization’s profitability. But often, maintenance, repair, and operations inventory are overlooked. This is in part because it’s nearly impossible to tie MRO inventory’s value and cost to a single item, and that “unquantifiability” can make MRO inventory tracking seem like more trouble than it’s worth.
But this is untrue. And, because MRO inventory is so frequently overlooked, many businesses are surprised to find real opportunities for cost savings in this category of supplies and materials. It also means that when MRO inventory optimization begins, companies can start saving time, money, and stress right away.
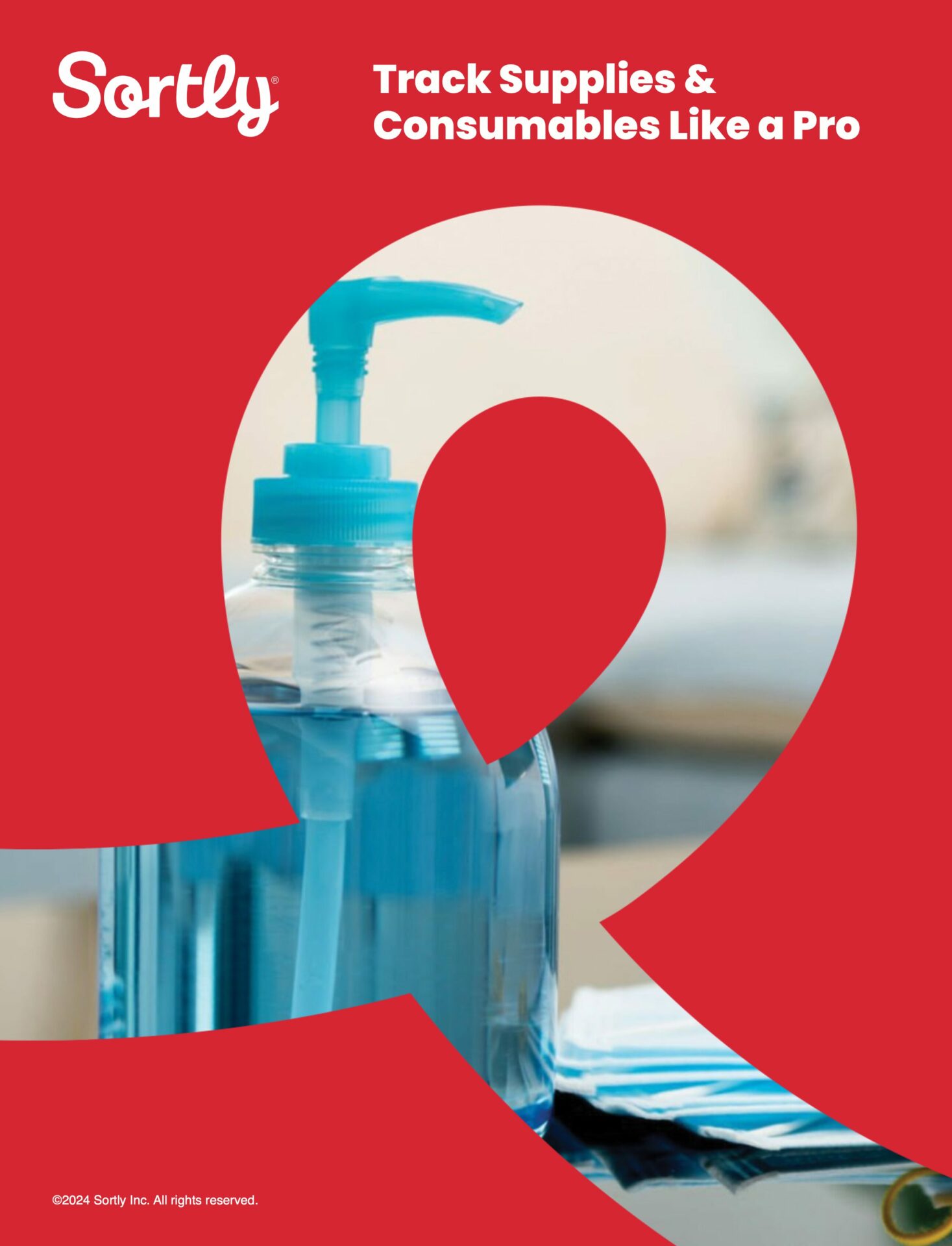
Free Ebook: Track Supplies & Consumables Like a Pro
This easy, comprehensive guide can help you:
- Create an inventory list for supplies and consumables
- Automate reordering with alerts and expiration reminders
- Perform inventory audits for consumable inventory
MRO inventory best practices
Like all other forms of inventory management and optimization, MRO inventory best practices are founded upon a thorough understanding of a company’s need, a top-notch physical organization strategy, a solid standard operating procedure that details how inventory is managed and tracked, and an ongoing commitment to inventory control. Here are five best practices to get you started:
1. Determine precisely what MRO inventory is needed
Whether you run a one-warehouse facility or a network of hundreds, the first step to truly optimized MRO inventory is defining what supplies and materials are needed to keep up with maintenance, repairs, and operations.
If you do not have solid data to forecast demand, you can look back at inventory records and purchase orders to determine a good starting point for future orders. Once you do this, you should oversee consumption for several weeks to months, determining your true business need.
If and when you implement a perpetual inventory management strategy that tracks MRO inventory consumption in real time, you’ll be able to refine this estimate with solid data within a few months.
Remember that your inventory minimum should include buffer and safety stock.
2. Improve how MRO inventory is physically stored and organized
The next step to optimizing your MRO inventory management strategy is ensuring that these supplies and materials are as physically organized and intelligently stocked as possible. This may mean an investment of time and new storage supplies from the onset. After all, it’s easier to kick start a truly optimized inventory strategy after first physically preparing your organization’s storage space.
From a single supply closet to hundreds of warehouses, ensure that all MRO inventory is placed in the most natural, easy-to-access, and auditable location.
3. Create a standard operating procedure
In inventory management, a standard operating procedure (SOP) articulates and formalizes how your organization manages all types of inventory, including MRO inventory. This document should include clear instructions about how inventory is stored and organized, how it is physically tracked and audited, how much of that inventory your business needs, and when, how, and from what vendors it is ordered.
4. Determine how inventory is tracked
This standard operating procedure should also clarify precisely how MRO inventory is tracked and managed within your organization. Typically, inventory is organized in one of three ways: manually, with a spreadsheet, or with inventory management software. Regardless of which platform you use, this standard operating procedure should detail all best practices regarding tracking all inventory.
Many businesses utilize inventory management software for its host of automation features, including low stock alerts and barcode and QR code scanning. Regardless of the size of your MRO inventory, practicing a perpetual inventory management strategy in which stakeholders understand exactly how much inventory is on hand at any given time and where that inventory is located can be very helpful.
That said, other businesses simply update inventory records at regular intervals, whether inventory data is stored on a sheet of paper, a spreadsheet, or an inventory software system.
Typically, the easiest way to track MRO inventory is how your business has decided to track all other inventory. So, if you’re considering upgrading to inventory software to track raw materials, WIP inventory, finished goods inventory, and other assets now, it’s wise to apply the same strategy to your MRO inventory.
5. Practice smart inventory control
Inventory control refers to the balancing act of ordering as little inventory as possible to keep costs low while ensuring there is enough inventory on hand to quickly meet customer demand. It’s a balancing act, and the more you know and understand your inventory usage, the better your ability to forecast demand and thus optimize inventory control.
Related: Sortly for Managing Supplies & Consumable Inventory
How to reduce MRO inventory
The above MRO inventory management best practices can be applied to your MRO inventory strategy to help reduce MRO inventory kept on hand. After all, by physically organizing this inventory, your team will be able to better understand how much MRO inventory is truly needed to keep operations running.
Then, they can apply that knowledge to all inventory-related decisions, from crafting a standard operating procedure to selecting an inventory management tracking system to implementing an airtight inventory control strategy.
About Sortly
Sortly is an inventory management solution that helps you track, manage, and organize your inventory—including MRO inventory—from any device, in any location. We’re an easy-to-use inventory software that’s perfect for large or small businesses. Sortly builds inventory tracking seamlessly into your workday so you can save time and money, satisfy your customers, and help your business succeed.
With Sortly, you can track inventory, supplies, parts, tools, assets like equipment and machinery, and anything else that matters to your business. It comes equipped with smart features like barcoding & QR coding, low stock alerts, customizable folders, data-rich reporting, and much more. Best of all, you can update inventory right from your smartphone, whether you’re on the job, in the warehouse, or on the go.
Whether you’re just getting started with inventory management or you’re an expert looking for a more efficient solution, we can transform how your company manages inventory—so you can focus on building your business. That’s why over 15,000 businesses globally trust us as their inventory management solution.
Start your two-week free trial of Sortly today.