Construction is an industry full of lucrative opportunities. But with those opportunities come inherent risks that can lead to costly overruns, delays, safety incidents, and legal liabilities. To navigate these challenges successfully, implementing an effective construction risk management strategy is crucial.
What is construction risk management?
Construction risk management is the balancing act of identifying, assessing, and mitigating potential risks that may affect a construction project’s budget, timeline, safety, and general success. To reduce the inherent risk of construction, construction companies of every shape and size usually adopt some sort of construction risk management strategy.
Risk management in construction projects helps stakeholders:
- Understand and proactively address risk
- Safeguard ongoing and future projects from these identified risks
- Ensure every aspect of operations proceeds smoothly, safely, and as planned
Understanding construction risks
To preemptively address risk, construction stakeholders must know where and how to identify such vulnerabilities. While potential risks may be embedded into any aspect and a construction project, every organization should at least learn how to identify the following seven types of construction risks:
1. Financial risks
In construction, the most common financial risk is simple: losing money. This happens due to budget overruns, fluctuating material prices, challenges with funding and loans, and other unexpected costs. While not all of these risks can be controlled, reducing financial risk starts with accurate cost estimation, meticulous budget tracking, thoughtful decision-making regarding funding and loans, and tightly monitoring labor and supply costs using strategies like inventory control.
Repeatedly failing to mitigate financial risk can jeopardize a business’s short-term and long-term health.
2. Project risks
Project risks refer to challenges and liabilities unique to each project. This includes inadequate project planning, design flaws, last-minute scope changes, and insufficient resources to execute construction properly. Mitigating these risks requires construction stakeholders to work alongside other teams, including architects and designers, building owners and owners’ representatives, contractors and subcontractors, on-site employees, and raw materials and inventory suppliers.
When projects cannot be delivered as planned, construction companies may face many other high-risk consequences, ranging from project delays to actual litigation.
3. Schedule risks
Schedule delays put an entire project at risk, unearthing various other risks, including financial and legal. And, if work is rushed due to pressure on a schedule, safety, operational, and environmental risks may heighten, too.
Not every risk to a construction project schedule can be managed. That includes unavoidable delays in construction due to poor weather. California, for example, experienced more rain than Washington State in 2023, disrupting construction progress on the state’s high-speed bullet train.
However, most schedule risks can be mitigated from the start. This is especially true for challenges that arise from material shortages and labor disputes. To avoid “controllable” schedule risks, create a realistic work schedule for every employee and proactively manage inventory so that supplies, materials, tools, and machinery are in the right place at the right time.
Many construction companies also create contingency plans to account for unexpected schedule delays.
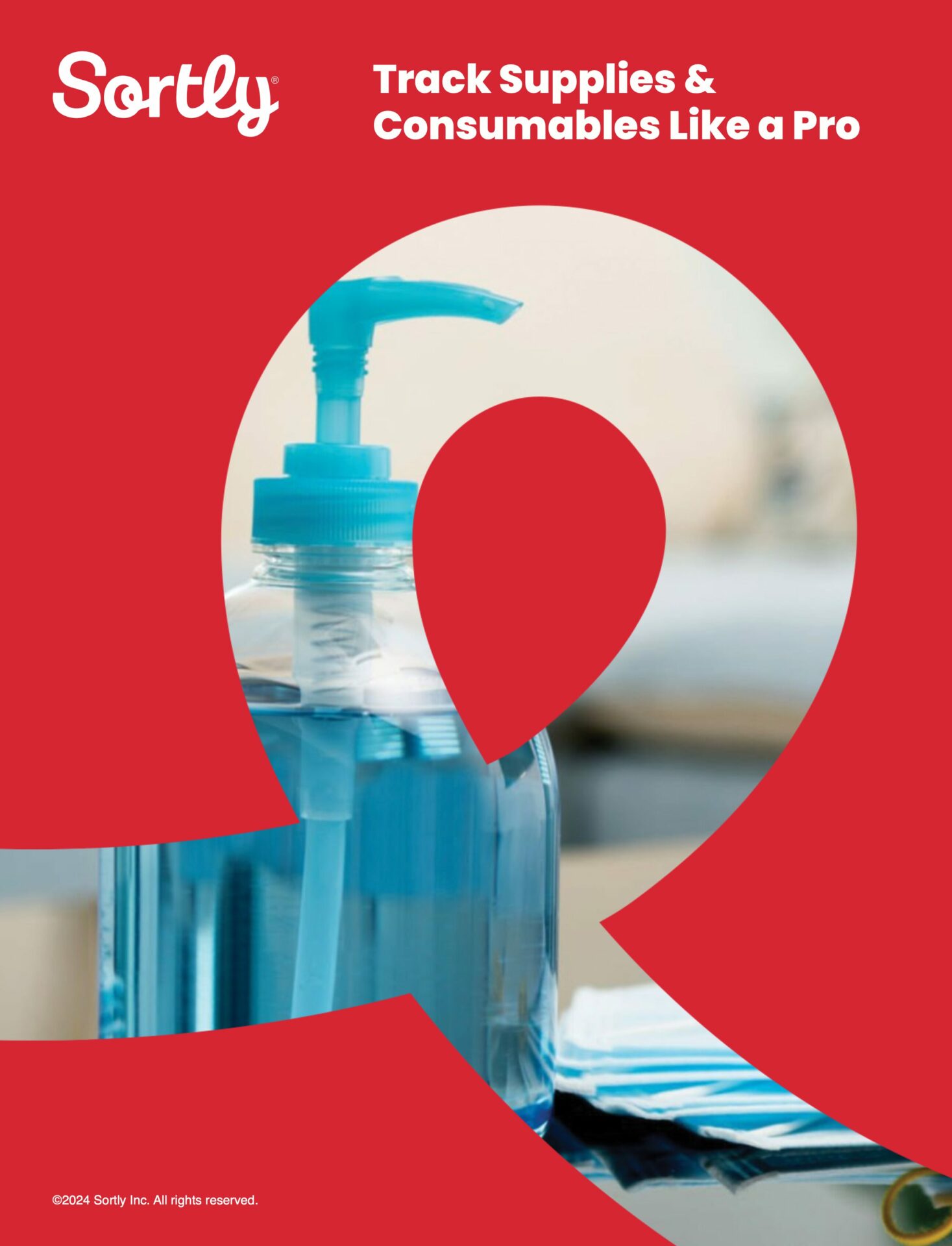
Free Ebook: Track Supplies & Consumables Like a Pro
This easy, comprehensive guide can help you:
- Create an inventory list for supplies and consumables
- Automate reordering with alerts and expiration reminders
- Perform inventory audits for consumable inventory
4. Operational risks
Operational risk refers to issues that arise as a result of construction activities. Activities that increase operational risk include poor communication, low-quality workmanship, equipment malfunction, and subpar quality control. These risks can affect a company’s ability to complete construction on time, safely, on budget, and as scoped.
To reduce operational risk, improve onboarding and offer frequent retraining of employees, optimize communication strategies, ensure quality control processes, and properly manage machinery and other assets using appropriate asset tracking software.
5. Safety risks
Safety risks are especially important to identify before a project begins. These risks directly affect on-site workers’ well-being and the safety of future tenants, custodians, and maintenance providers. During construction, safety risks include accidents due to inadequate safety measures and regulatory noncompliance. Examples include poor scaffolding and failure to require hard hats.
Failing to identify and mitigate construction safety risks can lead to accidents and incidents that cause bodily harm or death. Even without physical injury, construction projects that fail to address safety risks may be penalized and fined.
Validate safety compliance, implement rigorous safety protocols, offer ongoing retraining, foster a culture of safety awareness, and ensure guidance to all regulations. Consider implementing a QR code system for hazardous materials and machinery that allows on-site team members to rapidly learn more about safe handling, operating, and storing procedures.
6. Environmental risks
Environmental risks pose potential harm to a project’s surrounding environment. Such risks range from pollution and ecological damage to endangering nearby communities through improper waste disposal.
To mitigate environmental risk, understand precisely how construction operations could go wrong. Planning for the worst can help risk management stakeholders rapidly identify vulnerabilities and take appropriate precautions to keep the environment and community safe.
One example of environmental risk includes improper disposal of water used to clean cement mixers, paint mixing vestibules, or machinery. This water may contain toxins and chemicals that pose real hazards to the people and places nearby. Water should be bunded safely, then disposed of properly at a licensed facility.
7. Legal risks
Finally, a construction company may face legal risk if litigation arises from the consequences of any of the above six risks. Legal risks include contract breaches, disputes, regulatory violations, and more severe charges due to safety and environmental missteps.
Construction stakeholders should invest in clear and expertly-drafted contracts with partners, vendors, financiers, and customers to mitigate legal risk. Stakeholders should also adhere to local regulations, proactively handle disputes before they escalate, and carefully mitigate all risks at every phase of construction.
Related: 6 Inventory Tracking Methods for Construction Professionals
Risk mitigation strategies
While risk identification and awareness help executives and other top stakeholders see the bigger picture, a hands-on, company-wide risk reduction strategy is the best way to mitigate risk on the actual job site. Here are four of the top strategies construction companies implement to reduce risk:
1. Proactive risk mitigation
Identifying and addressing risks before they materialize or escalate is the most crucial element of risk mitigation. This strategy includes conducting thorough and frequent risk assessments, contracting with outside experts and agencies to evaluate hazards and vulnerabilities, and documenting identified risks and indicated actions to minimize them preemptively.
2. Risk response plans
For each identified rest, develop a customized response plan that outlines what steps will be taken if the risk materializes to minimize its impact. By creating a response plan before problems arise, your organization ensures it can deploy a swift, thorough, and well-coordinated reaction to events that would otherwise have seemed “unexpected.”
3. Contingency plans
One of the key secrets to mitigating risk is understanding that some issues will arise no matter how careful or thoughtful your risk reduction strategies may be. A contingency plan helps your organization prepare for potential disruption by allocating extra resources, time, and budget to a project. Contingency plans also offer your business a much-needed buffer during such events, helping projects stay on track even when roadblocks arise.
4. Collaborative risk mitigation
Finally, effective risk reduction requires construction stakeholders to work alongside other teams, including designers, owners, and subcontractors, to improve communication and collaboration. Together, all teams can align on risk mitigation to reduce individual and collective vulnerabilities.
Frequent meetings, especially when aided by the four real-time risk monitoring and control strategies outlined below, can help all stakeholders come together to mitigate risk.
Real-time risk monitoring and control
When reducing risk for construction stakeholders, consider implementing the following for touchpoints and strategies. These real-time risk monitoring and control tools allow construction companies to work alongside no project partners to identify, communicate about, and resolve risks before they become significant problems.
Technology-driven monitoring
Virtually all construction companies performing effective risk management utilize technology and monitoring tools. From 3D scanning software that allows remote stakeholders to compare what’s been built against what’s been planned to inventory management software that warns the right team members before essential raw materials run out, there’s no shortage of technology helping construction stakeholders reduce risk.
For example, consider a construction company that builds new homes across the tri-state area. This business may own several tractors, which are sometimes stored at headquarters and other times left on an active job site. The proper asset management software enables not only constant tracking of an asset’s condition and whereabouts but also safety and operating procedures. All of these features can help you reduce various risk factors, including safety, operational, and environmental.
Regardless of what technology is selected, ensure the necessary team members understand how to get the most out of these investments.
Early warning signs
Technology-driven monitoring can help construction stakeholders identify the earliest warning signs of risk before they escalate into major problems. Project managers should work together to regularly analyze data from the job site, including inventory lists, safety complaints, schedule progress, and design vs. reality visualizations.
The instant any sign of risk exceeds a company’s documented and established threshold, action should be taken. This is especially true for safety and environmental risks, where one mistake could prove irreversible. The sooner early warning signs of risk are addressed, the less likely a business will need to deploy contingency plans to handle them.
Regular risk review meetings
To make use of technology-driven monitoring, construction stakeholders on every side of the job should come together frequently to identify and review risk, put together contingency plans, discuss risk reduction strategies, and work together to ensure the safe, timely, on-budget, and as-designed completion the construction project.
These meetings can be virtual, in-person, or hybrid. Regardless of when they occur or where, all teams should focus on one goal: risk reduction. Meetings should be held internally and externally with other key project stakeholders.
Schedule these meetings well in advance, but also hold them as needed before and during construction.
Effective communication
Finally, the last key to significant construction risk is effective communication. Without frequent and transparent communication between stakeholders within your organization and externally.
For the hypothetical risks identified in the conference room to be mitigated on the actual job site, insist on constant communication, collaboration, and coordination between all stakeholders—from owner to inventory manager to drywall installer.
Experience the simplest inventory management software.
Are you ready to transform how your business does inventory?
Conclusion
Risk management is an essential aspect of construction that begins well before your next project breaks ground. To effectively reduce the chances that something goes wrong on one of your job sites, consider implementing a comprehensive, well-documented, and scalable risk mitigation strategy.
Continue to update this strategy with every lesson learned, new technology adopted, and project taken on. Over time, your risk mitigation will grow more intelligent, streamlined, and increasingly second nature to every stakeholder on the job.
Another important way to help mitigate risk is to stay on top of your inventory management strategy. Efficient inventory management can ensure you don’t lose money over or under-ordering construction materials, helps you avoid costly delays, and empowers you with the data you need for better planning. Learn more about how Sortly can help you transform your construction inventory management and sign up today.